Table Of Content
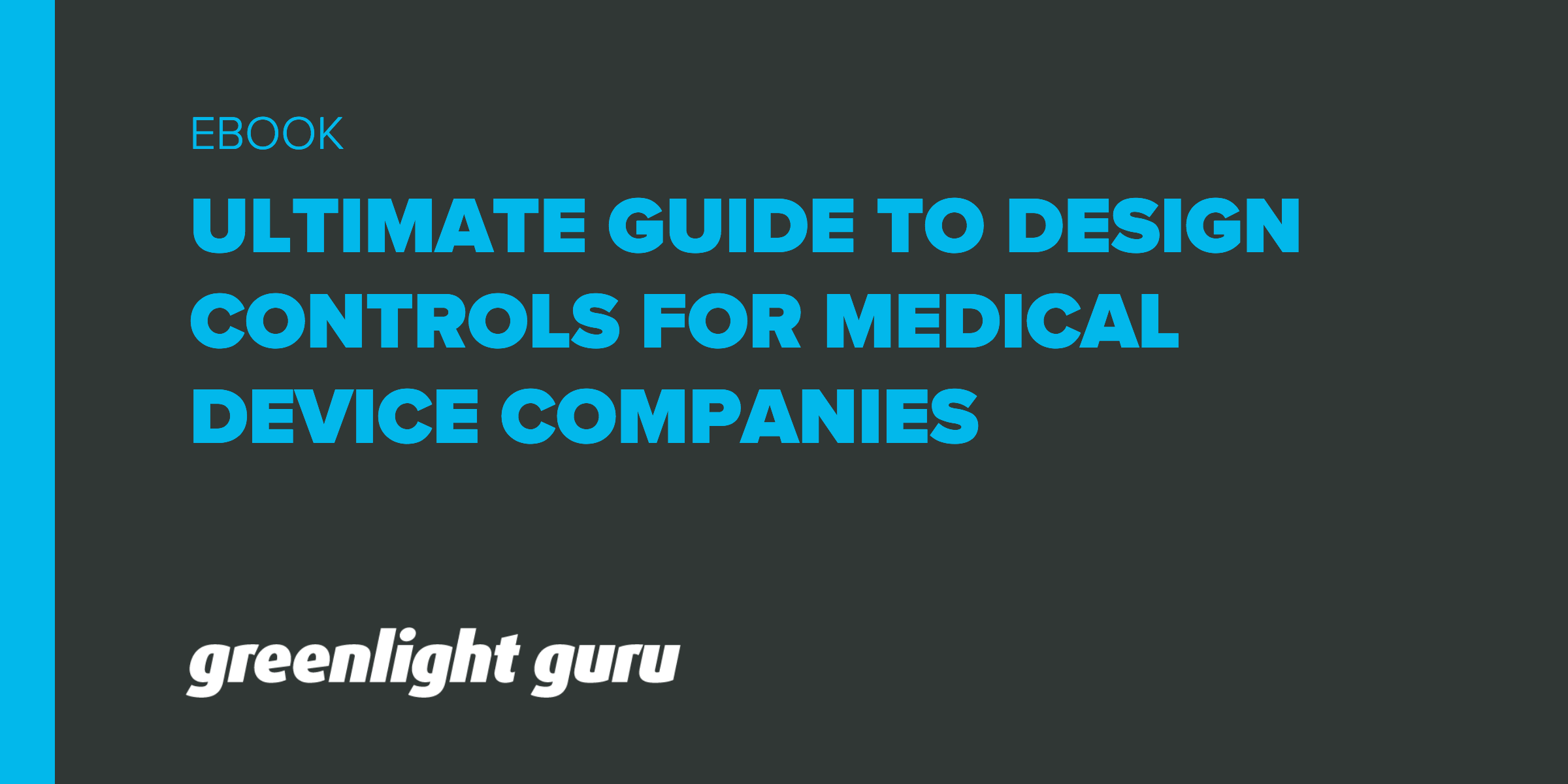
The aim is to provide a snapshot of some of themost exciting work published in the various research areas of the journal. Feature papers represent the most advanced research with significant potential for high impact in the field. A FeaturePaper should be a substantial original Article that involves several techniques or approaches, provides an outlook forfuture research directions and describes possible research applications.
How to Make Design Controls More Efficient: Here is a Tested Tool for Design Engineers
Design inputs are measurable design features that are intended to capture all functional, safety, and performance requirements. Similarly, the general purpose of design controls is to ensure that a suitable plan is in place for the development and production of a product. The design review process should account for risk analysis and change control where relevant. Design changes must also be validated unless the performance of only verification can be justified and documented by the firm. Where a design change cannot be verified by subsequent inspection and test, it must be validated.
Control circuit – simple design and engineering - Siemens
Control circuit – simple design and engineering.
Posted: Tue, 06 Feb 2024 09:08:37 GMT [source]
How do Design Controls Factor into a Quality Management System?
Food and Drug Administration (FDA) and International Organization for Standardization (ISO). This article will provide a perspective of how to use a blended approach to both. Design Controls are practices required by the FDA to facilitate a structured design and development process for medical devices. There are multiple checkpoints in place to ensure the device is safe and effective when brought to market. If you are a medical device manufacturer, compliance with Design Controls is required. In some cases, the design transfer may come before validation when your ability to produce a prototype or production-level device cannot be achieved in another manner.
Maintaining Device Master Record with Alternates and Substitutes
Regular design reviews and verification and validation activities are essential to confirm that the device meets its intended use and performance criteria. Managing changes and conducting rigorous design transfer processes are crucial for a seamless transition from development to manufacturing. Post-market surveillance and feedback mechanisms help manufacturers continuously monitor and improve their device designs based on real-world performance and customer feedback. The medical device industry manufacturers a range of technologies and applications, ranging from simple hand-held tools to more complex computer-controlled large surgical machines. While the guidance does not include a set of rigorous implementation methods, it consists of quality system requirements coupled with explanations and relevant design control principles examples.
The following elements are a generalized approach of blended FDA/ISO requirements, mostly using FDA terminology. Each element of Design Controls is carefully considered by an auditor, and those specific considerations are listed at the conclusion of each of the following Design Controls elements. Make sure that these things are planned and implemented early on so that every change is easier to understand.
Design input
If you haven’t already done so, migrate from a paper-based system to a cloud-based quality management system. These are now the industry standard, as they equip medical device companies to easily comply with ISO and FDA regulations. A paper-based system is cumbersome and makes it difficult to quickly log information in your DHF or communicate changes across teams. It can also leave more room for error, whereas in a cloud-based system, you can track changes, monitor who accessed a document, and more.

Design Controls, which are a systematic technique for developing Class II and Class III medical devices, are required by the FDA. This approach necessitates multiple layers of paperwork to show the FDA how you ensured the safety and efficacy of your medical device. The purpose of the Design Transfer phase is to implement procedures that safeguard correct design transfer from device design on into commercial production.
Risk Management is complex on its own, however, Risk Management is a critical part of all areas of design and development, and will be summarized here. Design Controls also ensure that a cross-functional approach is taken to the design process so that additional viewpoints are considered and potential roadblocks are realized early. You need to make sure that those making, moving, and installing the device have everything they need to do their job correctly. Section 820.30(h) from the FDA guidelines explains design transfer.
Just Terrible UI Design: This Freezer Control Dial - Core77.com
Just Terrible UI Design: This Freezer Control Dial.
Posted: Thu, 28 Mar 2024 07:00:00 GMT [source]
Most have adapted their own lexicon when it comes to medical device product development. Keep in mind that throughout medical device product development, the terminology used is grossly inconsistent and highly dependent on who is talking. The organization shall plan and control the design and development of product. As appropriate, design and development planning documents shall be maintained and updated as the design and development progresses.
If so, be sure you are aware of the challenges paper systems pose. Ensuring Design Controls documentation and records are stored in a DHF is very important. Yes, Design Controls and the DHF where these documents and records are maintained are important. A DHF should be organized and accessible to the entire project team. When you evaluate risks, you will need to establish Risk Controls to mitigate and reduce risks.
Validation activities must address the needs of all relevant parties (i.e. patient, health care worker, etc.) and be performed for each intended use. Validation activities should address the design outputs of labeling and packaging. These outputs may have human factor implications, and may adversely affect the device and its use. Determine if design verification confirmed that design outputs met the design input requirements. If design control requirements are applicable to the operations of the firm, select a design project. Unless the inspection assignment directs the inspection of a particular design project, select a project that provides the best challenge to the firm's design control system.
If a container cannot be identified properly by NIR, it has high probability of ending up in a landfill. Packaging features like color, labels, additives and more can impact a packages ability to be identified. With trinamiX, brands can assess the impact of these features to provide insight into product recyclability early in the design process. By designing packaging with recyclability in mind, manufacturers can help to reduce the amount of plastic waste that ends up in landfills. This is a crucial step towards creating a more sustainable and circular economy. With direct control over updates, rapid deployment of security patches isn’t just a pipe dream—it’s reality.
Risk analysis should be addressed in the design plan and risk should be considered throughout the design process. Review the design plan for the selected project to understand the layout of the design and development activities including assigned responsibilities and interfaces. The requirement for software validation is included in Section 820.30(g) Design Validation. However, if the project selected involves a device that contains software, consider reviewing the software's validation while proceeding through the assessment of the firm's design control system. Do not inspect a device under design control requirements to determine whether the design was appropriate or safe and effective.
If you press me to provide a definitive response to this question, I will defer to what is suggested by the Design Controls waterfall diagram. Do realize that one day in the future, you will need to demonstrate that the product you develop addresses the User Needs you define. When you read FDA Design Controls regulations, the part about DHF is mentioned towards the end. In fact, using Risk Management as a real tool will help you with Design Verification and Design Validation planning. With Design Controls, you also identify, evaluate, analyze, assess, and mitigate potential product issues. The intent behind Risk Management is to identify, evaluate, analyze, assess, and mitigate potential product issues.
It is very critical for every medical device company to follow the design control procedures set by the FDA (21 CFR 820.30) and properly document all of their activities accordingly. Each manufacturer shall establish and maintain procedures for verifying the device design. Design verification shall confirm that the design output meets the design input requirements.
Design control does not, however, apply to the ideation stage of medical device development. You don’t need to document the development of prototype concepts or feasibility studies. However, you do need to start creating a plan once you have decided that a specific design will be developed. To assist regulators, you should document the flow of the design process so it is very clear where research is ending and development of the chosen design is beginning. The length and detail of your design planning activities will depend on the product you’re planning to make and size of your organization.
No comments:
Post a Comment